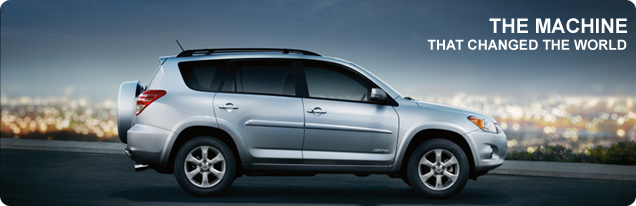
By Kiran Walimbe
How Mistake Proof Are Your Processes?
Poka Yoke, also called mistake proofing, is a simple method to prevent defects from occurring in your business processes. Learn from these three poka yoke examples.
It was a Japanese manufacturing engineer named Shigeo Shingo who developed the concept that revolutionized the quality profession in Japan. Originally called "fool proofing" and later changed to "mistake proofing" and "fail safing" so employees weren't offended, poka yoke (pronounced "poh-kah yoh-kay") translates into English as to avoid (yokeru) inadvertent errors (poka). The result is a business that wastes less energy, time and resources doing things wrong in the future.
What Is Poka Yoke?
Poka yoke is one of the main components of Shingo's Zero Quality Control (ZQC) system -- the idea being to produce zero defective products. One way this was achieved is through the use of poka yoke; a bunch of small devices that are used to either detect or prevent defects from occurring in the first place. These poka yoke methods are simple ways to help achieve zero defects.
Who Develops Poka Yokes?
Here's the beauty of the methods...anyone, from manager to line supervisor to line employee can develop a poka yoke. (Alright for you transaction people out there...anyone, from regional sales manager to sales associate to document specialist). All it takes is the empowerment of employees, as well as a little instruction around what makes a good poka yoke.
What Does A Poka Yoke Look Like?
Poka Yoke looks different in each situation. I'll try to present a few different scenarios for poka yoke use. Let's take a transactional situation and analyze a few parts of it. Say, for instance, we're at the signing of a bank loan by a lucky couple closing the mortgage on their first home.
Example 1:
The lucky couple picks up the pen to sign, but when they depress the top of the pen to extend the writing part it malfunctions because the spring is missing. A poka yoke could have prevented this situation. If all pieces of the pen were presented to the assembler in a dish, a simple poka yoke would be for the assembler to visually inspect the dish for any remaining parts once the pen was assembled. (Ok, I lied about this being only a transactional process!)
Example 2:
The lucky couple bypasses the signature part of the process because their bank is really high-technology focused. In fact, they signed a writing pad and their signature was recorded electronically. The bank also needed to collect 4 additional pieces of information before the entire package of information is sent to the processing department. A simple poka yoke to add to this process is to require all fields to be filled in (including the loanee signature) before allowing the form to be sent to processing. This prevents the processing department from reviewing an incomplete document, sending back to the loan department, delaying the processing of paperwork...you get the idea.
Example 3:
Once the complete paperwork is submitted to the processing department and it is printed, it then needs to be filed with the city and state. In order for this to occur, papers need to be filled out (the city and state are not high-technology enabled) and attached to the form. A poka yoke used by the city is a simple check-sheet at the top of the form. This allows the person submitting the form to ensure that all additional information and payments are attached. As in example 2 above, this prevents the city/state from reviewing an incomplete document, sending back the document to the sender, delaying the processing of paperwork...again, you get the idea.
Conclusion
Is there any rocket science to poka yoke? I don't think so either. So what's the big deal? Well, the big deal involves execution within your business. Bright ideas are a dime a dozen, it's the execution that's the hard part. First, you need to educate your workforce on the concept of poka yoke (call it mistake proofing for ease). Second, you need to empower your employees to make a bunch of small improvements to their processes -- continuously. What you will end up with a business that wastes less energy, time and resources doing things wrong in the future.
Work Instructions for Mistake Proofing
This step-by-step guide provides the directions for performing Poka Yoke techniques to processes.
1. Use CFT approach to Mistake proofing.
2. Selection of process for Mistake proofing.
During the third phase of APQP, the CFT shall identify the processes, where, due to avoidable human errors, the rating of "Occurrence" and/or "Detection" have increased thereby increasing the RPN for the process. Poka Yoke techniques of mistake proofing are applied to these processes in order to lower the ratings of Occurrence and / or detection.
Analysis of Customer complaints also reveals activities which are in need of mistake proofing, in order to achieve 'Zero Defect' level of working. CFT will undertake application of Poka Yoke techniques to these processes.
3. The selected mistake proofing technique should qualify the following criteria:
• Inexpensive
• Based upon common sense, preferably of the operator or the 1st line employee
• It MUST eliminate Occurrence / Detection of the problem at the source itself
4. Occurrence oriented Poka Yoke should follow the procedure as below:
First classify the source of 'Occurrence' as follows:
• Required action is NOT performed or is performed incorrectly.
• Undesired action is exercised.
• Information essential for performing the action is mis-interpreted.
• Mistake occurs due to complexity.
After having classified the source, apply one of the following techniques, as appropriate, to prevent the occurrence:
• Use of 100% prevention devices such as Fouling Pins, Contoured locators or templates, Proximity or Photo-electric sensors, Limit or Micro switches, Warning lights or Buzzers, Pressure transducers.
• Design to modify to ensure that in assembly the parts shall not join if aligned wrongly. Machine will not run if operators' hands or feet are not outside or if the job & tooling are not in right position.
These techniques should be integral part of the process. The devices are placed sufficiently close to where the mistakes occur, providing fast feedback to the operator, of mistakes occurring.
5. Detection oriented Poka Yoke should use one of the following techniques for ensuring 100% detection of the mistake:
• It should be autonomous inspection occurring without intervention.
• It should be 100% inspection which occurs without intervention.
• It should determine 'before the fact' whether the conditions for 100% quality exist or not.
• It should make the error visible to the operator.
• Consider supply of exactly made kits of components to the assembler, so that any balance part will signal error in assembly.
• Consider use of electronic sensors to activate warning lights or buzzers.
• Use colour coded parts or graphics.
• Make use of contact devices e.g. Fixtures, Limit switches, probes or Non-contact devices e.g. LEDs, Pressure transducers etc.
6. Effectiveness of the applied Poka Yoke technique should be judged after observing the performance, for a period on minimum one month.
» More Information